认 证:工商信息已核实
访问量:2365939
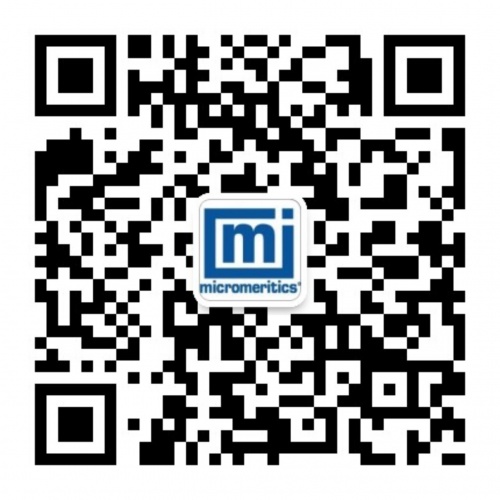
麦克默瑞提克(上海)仪器有限公司 2020-09-30 点击771次
粉体混合物的加工通常会面临诸多的挑战:部分粉体在加工过程中流动性较差,混合物容易分层或团聚成块,影响混合的均匀性。因此各行各业广泛运用造粒改善这一问题,造粒是将多种不同的成分混合加工成自由流动、均匀的中间体,供下游加工使用。通常采用湿法造粒,得到湿颗粒后进一步干燥、研磨。过程耗时且昂贵,并且某些API易热降解,难以造粒。
干法造粒能够减少加工工序、降低整体成本,具有巨大的优势,并且可用于热敏感材料。难以确定哪些工艺参数能够取得好的质量,实现连续化生产并获得高质量的产品。因此,大多数设备供应商和制药公司只能凭借经验和测试结果确定合适的参数。

实验方法
对照品使用70% 乳糖、29.5% 微晶纤维素和0.5% 硬脂酸镁通过Gerteis MINI-PACTOR® 辊压机造粒而成,其中压辊间距、挤压力和压辊速度可根据筛网尺寸调整。得到的干燥颗粒使用英国富瑞曼科技 FT4 粉体流变仪™进行评估,量化动态、整体和剪切属性。
挤压力的影响
MINI-PACTOR® 采用不同的挤压力处理六批相同的原料:

压辊间距保持在3 mm,压辊速度为2.5 RPM,筛网尺寸为1 mm。得到的六批颗粒随后使用FT4 粉体流变仪™进行评估,研究挤压力对颗粒属性的影响。
预处理后的松装密度和可压性
根据结果观察,干颗粒预处理后的松装密度 (CBD) 和可压性与挤压力为线性关系,挤压力越大,CBD越大,可压缩程度越小。
挤压力越大,得到的颗粒越均匀,内部能够更高效地排列。这种高效堆积性能能够降低孔隙,提高松装密度,颗粒受应力作用可移动的空间减少。
透气性
根据结果观察,透气性和挤压力之间存在相关性,挤压力越大,透气性越好。
如果使用较大的挤压力生成颗粒,获得更耐压的粉体。也就是说,当粉体受到外部应力时,可以维持颗粒间通道,以便空气自由流通。
结果显示挤压力与松装密度、透气性和可压性之间存在直接的相关性。随着挤压力增大,可压性降低,透气性和松装密度增大。这些属性都是高效堆积的标志,自由流动的材料通常具有此类的特性。
与动态流动和整体数据相比,剪切特性几乎无影响,测试结果显示样品之间几乎不存在差异,并且壁面摩擦角和挤压力之间不具有相关性。剪切盒主要评估连续、粘性粉体在高应力条件下开始流动的情况,因此与动态、低应力过程无关也是合理的。
压辊间距的影响
MINI-PACTOR®采用不同的压辊间距处理六批相同原料:
挤压力保持在4.5 kN/cm,压辊速度为2.5 RPM,筛网尺寸为1 mm。得到的六批颗粒随后使用FT4 粉体流变仪™进行评估,研究压辊间距对颗粒属性的影响。
预处理后的松装密度
颗粒松装密度随压辊间距的增大而减小,这表示间距越大,所得颗粒的一致性越差,粒径分布较宽。粒径分布较宽的材料通常堆积效率较低,易于夹带空气,松装密度降低。
固结指数和透气性
根据结果观察,固结指数和透气性与压辊间距之间存在一定的关系,压辊间距越大,对振动固结越敏感,透气性也越低。
这也证明如果压辊间距较大,颗粒粒径分布较宽,导致内部重排,堆积不均匀,内部夹带较多的空气。受到振动作用时,颗粒重新排列,堆积成更有效排列的结构,排出空气,流动能明显增大。此外,如果堆积结构不均匀,无法构建稳定的空气通道,可能致使透气性降低。
随着压辊间距增大,压辊之间形成的固结部分不一致,得到的颗粒也不均匀。很可能导致颗粒粒径分布、形状和表面结构出现较大的差异,最终颗粒的堆积效率降低 (得到高固结指数、低透气性和低松装密度的结果)。
挤压力和压辊间距的变化
使用不同的挤压力和压辊间距得到九批相同原料的干颗粒,与仅改变压辊间距或挤压力的结果比较,考察是否遵循相似的变化趋势。

预处理后的松装密度和可压性
与4.5 kN/cm挤压力相比,使用9 kN/cm挤压力在不同压辊间距下生成的颗粒松装密度更大,可压性更低,与最初结果吻合。比较4.5 kN/cm和9 kN/cm的挤压力下,压辊间距和松装密度之间的线性关系,表明压辊间距和松装密度之间的关系与挤压力无关。但压辊间距和可压性之间的关系并非独立于挤压力。在9 kN/cm挤压力的作用下,可压性随压辊间距的增大而急剧上升,说明在较大的挤压力下,压辊间距对颗粒属性的影响更明显。
透气性
与4.5 kN/cm挤压力相比,使用9 kN/cm挤压力下生成的颗粒透气性更好,表明较高的挤压力下,生成颗粒内部排列更均匀,透气性更好。这一结果也验证了之前观察到的压辊间距与透气性之间的关系,但在较大的挤压力下,曲线的斜率更大,进一步证实了高挤压力下压辊间距对颗粒属性具有更大的影响。
结论
“质量源于设计”的理念要求充分理解材料和加工过程之间的关系,以便能够控制和优化工艺性能,确保最终产品的质量。以上结果证明,我们可以通过确认关键工艺参数优化辊压造粒的过程,生成颗粒的特性会直接影响下游操作性能和终产品的关键质量属性。
根据观察,FT4测得的流动特性存在明确、可重复的趋势,展示了工艺参数如何对颗粒流变特性产生可预见性的影响。样品的透气性、可压性和预处理松装密度与辊压机的运行模式存在明显的相关性,总之,较小的压辊间距配合较大的挤压力能够产生更均匀、一致的颗粒,形成更高效堆积的粉体,促使其自由流动。
该研究展示了粉体流变学在全面、多变量粉体特性表征方法中的价值。流动性并非材料的基本属性,它反映的是多种属性对于粉体在特定设备中整体表现的影响。某些属性的微小差异可能导致工艺性能发生显著的变化,这意味着需要采用多种特性表征方法,所得出的结果能够与过程评价相关联,从而获得对应于可接受的工艺特性的参数设计空间。
共同作者
感谢我们的合作伙伴Hartmut Vom Bey和Michael Hanisch,更多信息请访问Gerteis Maschinen+Processengineering AG。